Macroscopic Scale
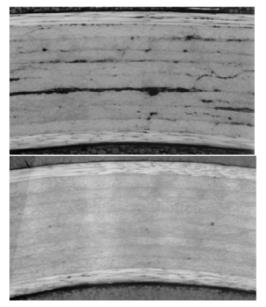
hilighting the transverse crushing during forming process
The main goal of this approach is to develop numerical tools to simulate the forming of continuous fibre composite reinforcements and prepegs at the macroscopic level at reasonable computational times. At this scale, the structure is considered as a continuum medium, where the first proposed hypotheses assumes the fibres are inextensible and can slip between each other, while the second includes transverse crushing for consolidation. The behaviour of the material assumes membrane, bending and transverse shear.
From these assumptions, the displacement, deformation and the strain/stress variables are modelled and the parameters of the behaviour laws are identified. In a first stage, shell elements will be implemented with bi-dimensional geometry with the choice of a two-dimensional geometry (triangular, quadrilateral elements) and an order of geometric approximation (linear, quadratic), with an emphasis on the locking phenomena encountered in shell finite elements. Classical validation tests (elementary testes, rank, etc.) will be used to verify the correct implementation. Solid-shell elements will then be developed, allowing for the inclusion of the second main assumption (transverse crushing) as shown on the FE reference configuration below
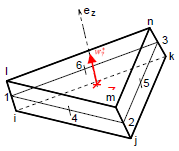
Again, with choices regarding the now tri-dimensional geometry (tetrahedral, hexagonal elements) and order of magnitude (linear, quadratic), with the same emphasis on the locking phenomena and with the same validation tests. At last, simulation of representative tests of the shaping of fibrous structures will be carried out: draping with different stacking (varying both orientation and number of layers); compaction and consolidation of the solid-shell. These tests will be implemented experimentally.
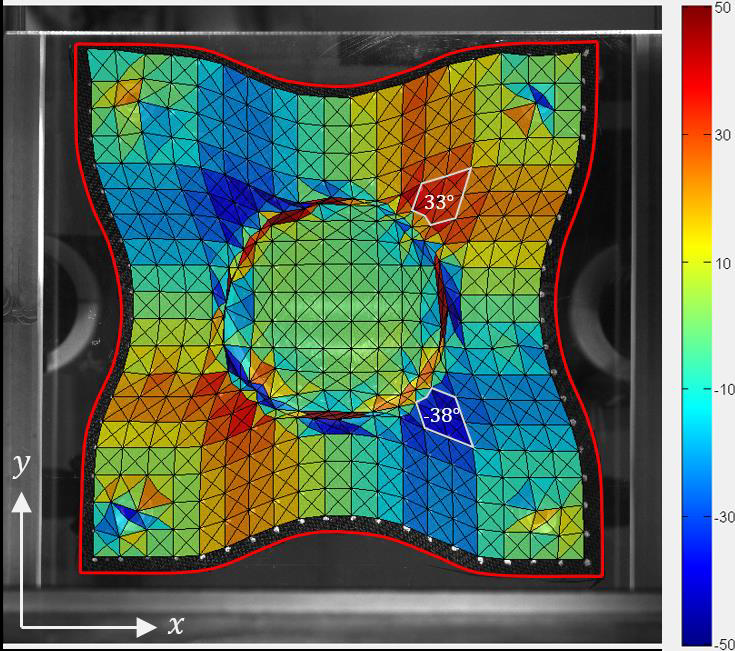
cells of a multilayer textile during hemispherical forming
Mesoscopic Scale
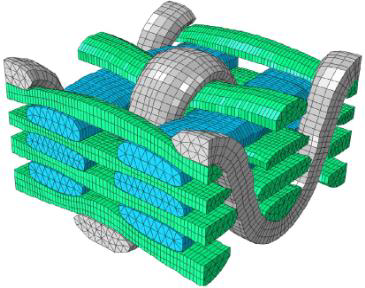
At the mesoscopic scale we consider every yarn as a deformable solid interacting with its neighbors. Thus this scale of representation allows to simulate specific behaviors such as buckling and compaction of yarns but also to measure gaps between each other. Usually, at the mesoscopic scale, the model of the textile is done on a Representative Volume Element (RVE) which takes into account the periodicity of the weaving. However, even if the number of yarns is reduced, classic 3D elements model often are computational time non cost-effective.
Therefore, the aim is to develop an element based on a solid-beam formulation which will be representative of yarns’ fibrous behavior and cross-section deformation. Macroscopic hypothesis such as quasi-inextensibility of fibers and their relative slipping will be extended to mesoscopic scale, which means that this implemented beam kinematics will be specific to fibrous yarns. Also this element will be able to deal with yarn-yarn contact and friction, moreover, to insure its robustness the emphasis will be put on locking phenomenons.
To validate this new finite element the collaboration with Laboratoire de Physique et Mécaniques Textiles will allow to compare simulation and experiment. First on elementary tests with only yarn such as yarn-yarn friction or yarn compaction, and then on forming process with entire textiles to compare results on yarn’s gaps and buckling.
Finally, to give a better global understanding of this project, we will carry out a comparison with macroscopic approaches developed by Laboratoire Energétique Mécanique Electromagnétisme. Indeed, this final step will define the use perimeter of each modeling type and their outputs in order to propose a multi-scale analysis.
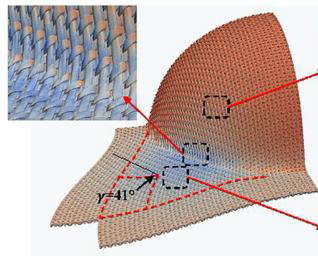
warp and waft yarns during a hemispherical forming process
Experiment and Characterisation
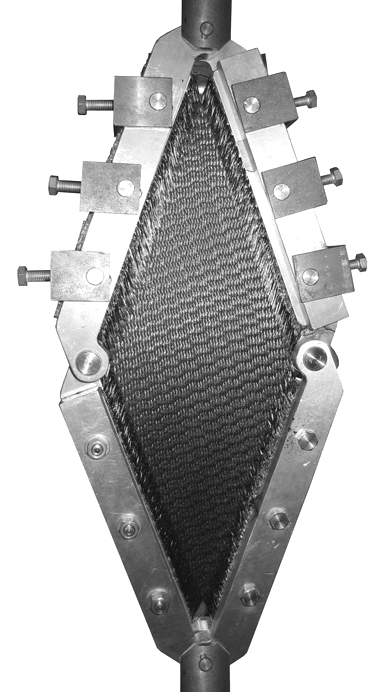
The goal of this project is to develop tools to simulate the composite shaping process called Resin Transfer Moulding. The project focuses on two different scales: the mesoscopic scale studying the behaviour of the yarns and their interaction during the forming process, and the macroscopic scale describing the behaviour of the fabric during the forming process.
Several materials were picked to represent the forming process. In order to simulate these materials, their properties must be quantified. Measures are conducted on simple deformations such as tension, in-plane-shearing, flexion, etc. These simple deformations are then coupled together thanks to the behaviour laws to describe better what is really happening during the process.
These measures will be conducted at room temperature and at forming temperature (around 180°C for the chosen materials) to be ask close as possible to the forming process. In addition to the simple deformations, some tests will be conducted to explore the coupling of the properties (bending of a sheared fabric for example).
To make sure that the simulations are correctly describing the behaviour of the materials, validation measures will be set up. Some shapes such as non-developable surfaces are known to cause defaults during the forming process. Dies with such shapes will be produced and be used to punch the fabric to deform it. The measures on the deformed fabric will then be compared to the simulations’ results and allow to validate them.
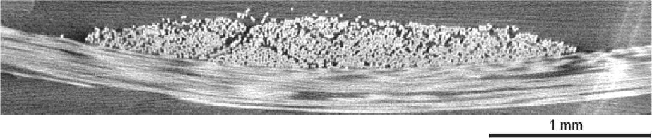
