Forming simulation of variable-thickness continuous fibre composite reinforcement at the macroscopic scale
Composite materials offer a lightweight structural alternative to the metals traditionally used in the aeronautical and automotive industries, leading to fuel savings that reduce the carbon footprint and increase overall performance. Naturally, this replacement of the base material comes with different manufacturing processes, where specific mechanics take place.
Liquid composite moulding processes for dry textiles [1] (figure 1a) and thermoforming of prepregs [2] are two particularly interesting forming processes. They are used for continuous fibre composite reinforcements (CFCR) when the resin is yet to be injected/hardened and are able to deliver a high volume of structural parts. The preform is draped by a mould, producing complex shapes, often with double curvature (figure 1b). These processes, however, still require a lot of expensive trial and error tests in the design phase, as different final designs need to be tested to assess the feasibility of a desired shape. Numerical tools replace this expensive testing, reducing the manufacturing cost and expanding the available design options. These tools should be able to not only predict the final fibre orientation, but also
predict the appearance of possible defects such as warping and fibre sliding/fracture. Incorrect fibre orientation and/or excessive defects (in particular warping) can lead to poor final properties: not only is there a stiffness loss, but the permeability is also reduced, creating voids where the resin cannot flow into.
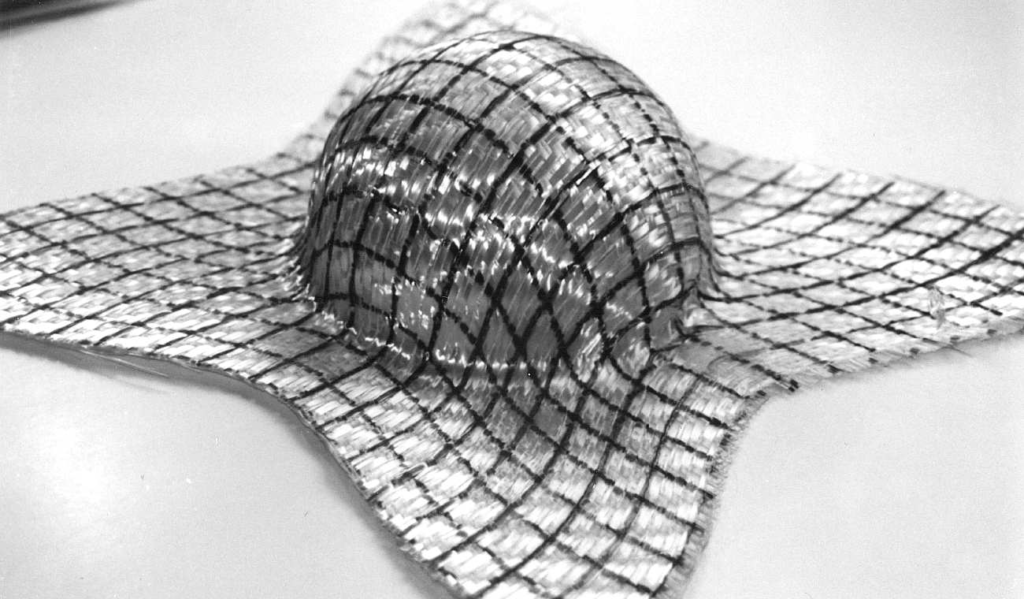
(a) Resin transfer moulding [1]
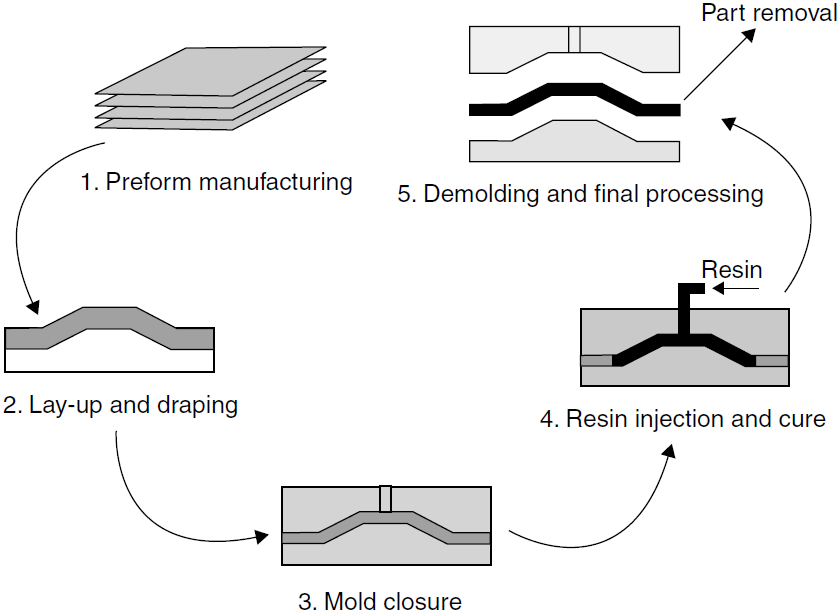
(b) Double-curved shape [3]
The mechanical behaviour of CFCR materials is complex and characterised by interactions at multiple scales: at the microscale, millions of microscopic fibres of a given material form a yarn; at the mesoscale, visible yarns are processed into different weaving patterns; at the macroscale, the reinforcement is draped into a complex shape. In this work, we focus on the deformation at the macroscale, where the material properties are defined by the different phenomena that occur at the smaller sizes. At this scale, the deformation of the preform is driven by four different mechanisms [4]: inter-fibre shear (change of fibre orientation), inter-fibre slippage, fibre buckling and fibre extension (small due to high stiffness). When stacked, specific deformation occurs [5], due to the high stiffness in the fibre direction and an absence of a binding agent between the plies (allowing inter-ply slippage): initially normal
lines to the mid-surface do not necessarily remain normal to it and plies can curve even when the initial normal lines do not rotate; at the same time, the thickness does not remain constant; thus not being describable by Kirchhoff nor Mindlin hypothesis.
The simulation of CFCR can be divided into two types of models: continuous and discontinuous. Discontinuous models describe more accurately the process, but require each individual yarn and interaction to be modelled, resulting in a computationally expensive model at the macroscale. Continuous models, while less accurate and unable to predict inter-ply slippage, present a less expensive alternative where the mechanical behaviour is driven by the principal (fibre) directions. In this talk, we will present a specific continuous finite element for laminate stacks with variable thickness.
References
[1] E. M. Sozer, P. Simacek, and S. G.Advani, Resin transfer molding (RTM) polymer matrix composites, Manufacturing Techniques for Polymer Matrix Composites (PMCs)
245-309.
[2] D. H. – J. A. Lukaszewicz and K. D. Potter, The internal structure and conformationof prepreg with respect to reliable automated processing, Composites Part A: Applied
Science and Manufacturing 42 3 (2011) 283-292
[3] B. Liang, and P. Boisse, A review of numerical analyses and experimental characterization methods for forming of textile reinforcements, Chinese Journal of Aeronautics 34(8) (2021) 143–163
[4] C. D. Rudd, A. C. Long, K. N. Kendall, and C. G. E. Mangin, Liquid molding technologies, Woodhead Publishing, in Cambridge: SAE International, (1997)
[5] B. Liang, J. Colmars, and P. Boisse, A shell formulation for fibrous reinforcement
forming simulations, Composites Part A: Applied Science and Manufacturing 100
(2017) 81-96