A solid-beam approach for mesoscopic analysis of textile reinforcements forming simulation
Keywords : solid-beam, hyperelastic, mesoscopic scale, fibrous finite element
Background
Finite element analysis of meso-scale textile reinforcement models faithfully reproduces defects like yarn buckling or gapping during the forming processes. They are often based on accurate geometric models very finely meshed or high-order interpolation elements. It leads to high fidelity results regarding experiments, but also numerically expensive response. Conversely, coarser modelling, while enabling faster computation, usually includes assumptions which do not consider the fibrous behavior of textile reinforcements.
Procedure
This study proposes a solid-beam fibrous element formulation based on a hexahedral element with 4 beams attached to its edges, which represent the fibers of the modelled yarn.
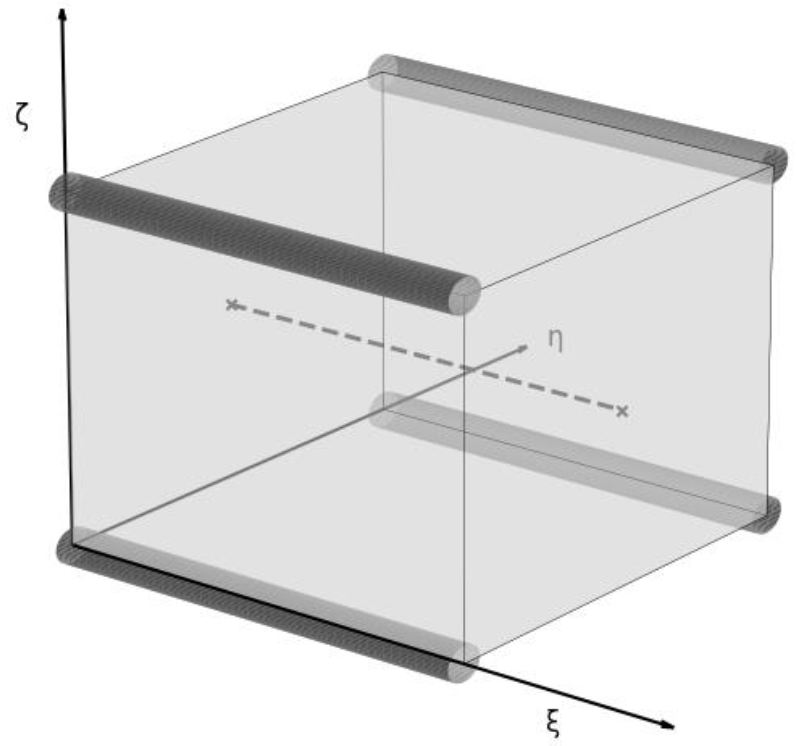
The dedicated fibrous finite element formulation is based on phenomenological observations: behavior of textile is mainly guided by quasi-inextensibility of fibers and their relative sliding or rearrangement [1].
Beam’s bending behavior is handled thanks to a 3D adaptation of the Neighbor Element Method [2]. An enhanced version of transverse isotropic hyperelastic law [3], which takes into account the fiber volume fraction, is applied to the hexahedral element material behavior.
Validation is done through comparison with experimental tests and other mesoscale models.
Key Findings
- An efficient and cost-effective finite element formulation to determine gapping and yarn misorientation in textile reinforcement forming processes.
- Fiber volume fraction field at the mesoscale as a direct output of the simulation.
References
[1] R. Bai, J. Colmars, N. Naouar, et P. Boisse, « A specific 3D shell approach for textile composite reinforcements under large deformation », Composites Part A: Applied Science and Manufacturing, vol. 139, p. 106135, 2020, doi: 10.1016/j.compositesa.2020.106135.
[2] B. Liang, J. Colmars, et P. Boisse, « A shell formulation for fibrous reinforcement forming simulations », Composites Part A: Applied Science and Manufacturing, vol. 100, p. 81-96, 2017, doi: 10.1016/j.compositesa.2017.04.024.
[3] A. Charmetant, E. Vidal-Sallé, et P. Boisse, « Hyperelastic modelling for mesoscopic analyses of composite reinforcements », Composites Science and Technology, vol. 71, no 14, p. 1623-1631, 2011, doi: 10.1016/j.compscitech.2011.07.004.
Article de la conférence